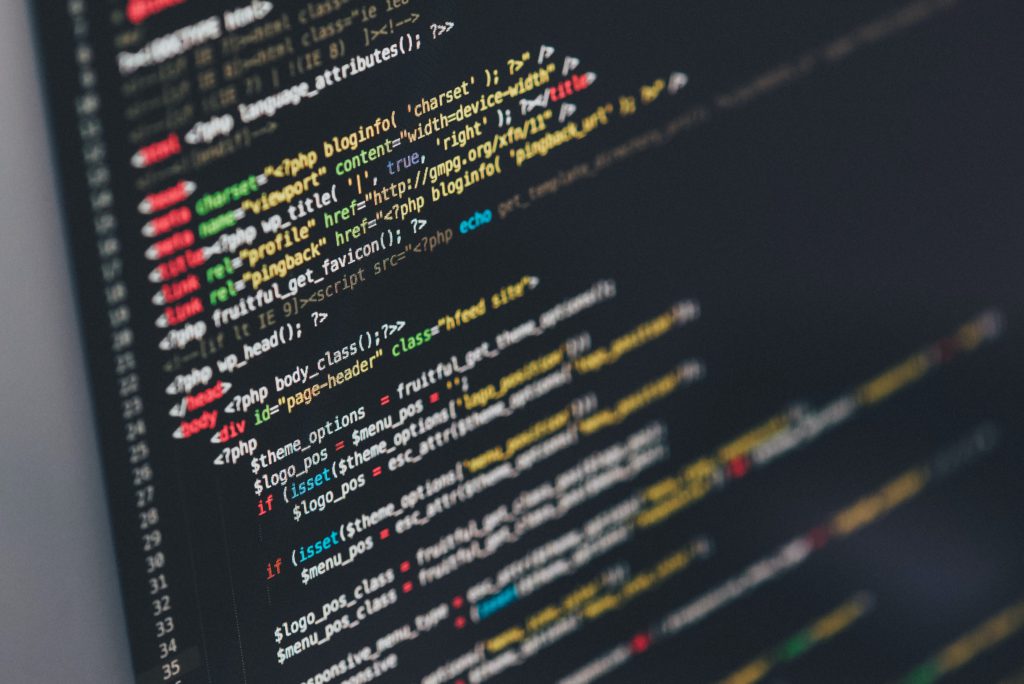
Photo by Ilya Pavlov on Unsplash
Description
Deploying robotic process automation (RPA) technology to free-up human capacity and creativity .
Context
The British Red Cross creates a vast amount of information as it helps people in crisis, attracts new supporters, transforms its digital infrastructure, and recruits staff to deliver our ambitious vision for the future.
Data flows are critical for everything we do but our staff rely on a complex network of software, hardware and experience; information passes through multiple databases and intricate workflows. Processes often only exist in people’s heads or are not fully mapped at all.
Frustratingly, we require our dedicated, experienced people to spend a significant portion of their time finding and preparing data, transferring information between systems, and running routine checks manually. This reduces the value we get from their expertise and their enjoyment of work.
This situation has developed organically as technology has infiltrated all aspects of our work, with multiple platforms and applications required for most processes. Replacing legacy systems is a key workstream but it is costly and slow. Process improvement is hampered by the lack of time teams can dedicate to developing, testing and deploying new solutions because of the ‘heavy lifting’ they have to do to keep information flowing around the organisation. Our staff costs are growing but we are still overstretched in many areas.
Robotic Process Automation (RPA) technology could offer a cost-efficient way to add capacity to the organisation, reduce staff overheads and cut corporate risks by increasing accuracy and compliance checks.
We tested the following hypothesis by running a rapid experiment: “We can free-up time, money and brain power across the Red Cross by creating digital workers that automate routine processes and increase the value we get from our legacy system.”
Technical details & Operations
Robotic Process Automation (RPA) uses software, commonly known as a ‘robot’ or ‘digital worker’, to run processes using existing IT applications, following the same steps and using the same interfaces and access permissions as our staff. They can be trained to run complex processes at speed, with high accuracy. They can work 24 hours a day, with one bot licence operating several processes.
Multiple robots can be seen as a virtual workforce – new capacity which works alongside our staff and allows humans to concentrate our efforts elsewhere. One digital worker can be trained to help multiple teams, actively optimising its own workload. The can operate across departmental boundaries and organisational silos, increasing efficiency.
RPA technology is well established in the banking and insurance sector, and increasingly visible in Third Sector organisations such as Local Authorities, Heath Trusts and Housing Associations. But is not yet commonplace in the charity sector.
Evidence shows that the benefits of RPA adoption can be significant. Payback was reported at less than 12 months, with an average 20% of full-time equivalent (FTE) capacity provided by robots. Users also report improved compliance (92%), improved accuracy (90%), improved productivity (86%), cost reduction (59%). [Deloitte figures].
To assess the technology and verify that benefits realised in other industries would translate to the British Red Cross, a comprehensive proof-of-value (PoV) project has been run. This generated evidence for investment to roll out a new automation capability which will allow the BRC to deploy RPA effectively and create new capacity.
Deployment & Impact
In brief, the PoV has demonstrated that an RPA platform can be set up safely within our tech estate and work with our existing systems.
The initial results are positive. The first automation is working alongside the Accounts Payable (AP) team. It initially ran 5 high-volume suppliers, saving the team 90 minutes a day. Also, the speed at which suppliers were paid increased from 5 days to just 2. Time returned to the team was used to tackle account reconciliations and other outstanding tasks.
The robot – named Optimus by the team – is now being scaled to run the top 23 suppliers. These account for 25% of all invoices received. Automating at this scale will return significant time to the AP team.
Alongside this, an analysis of business-critical processes across the BRC illustrated that there are tens of thousands of hours of work which can be automated. A sample of 19 candidate processes were assessed in detail; these alone currently absorb over 17,000 hours of work, equivalent to 10 FTEs. Adding automation capability will give managers new options when developing strategy and budgets.
Based on this evidence, a new team is being set up to build automations using RPA technology. They will work with host teams and subject matter experts to identify key processes which are high cost, high volume and/or high risk. These will be automated. The human capacity freed-up by the deployment of RPA will be used to tackle backlogs, process improvements or other areas of work.